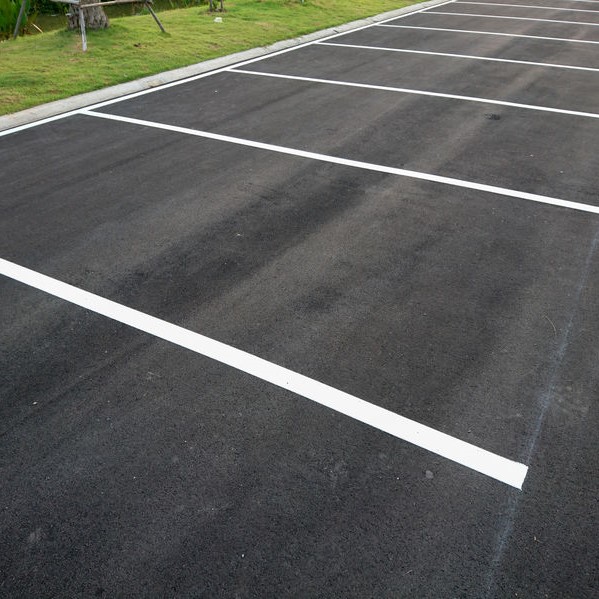
Parking lots and changing seasons
Winter is going to blast through that northern door any day now, and as a commercial property owner, you have several things to winterize, including the parking lot. Yes, in addition to pipes being wrapped and weather-stripping doors and windows, your parking lot needs winterizing too. It is part of basic parking lot maintenance that is overlooked too often.
What is parking lot maintenance exactly and why is parking lot maintenance needed? In America, more than ninety percent of all parking lots are asphalt, a material that damaged from weathering overtime. A unmaintained parking lot becomes damaged with cracks and potholes which can is unappealing and unsafe.
Parking lot maintenance involves keeping repairs done and performing treatments that extends the life of the parking lot. With consistent and proper parking lot maintenance, it will maintain your property value while ensuring the customers, employees, and other visitors a safe arrival and departure. So, just like with your lawn care at home, the parking lot maintenance and the seasons need to be a matter of routine too.
How do you maintain a parking lot?
There isn’t much to knowing how to maintain a parking lot really, it’s a matter of a few basic steps and knowing when you need professional services to the surface. Here, we offer the recommended steps to parking lot maintenance that will give you guidance on how to do parking lot maintenance.
Once you know how, you can schedule routine parking lot maintenance for your property and get the most out of that asphalt parking lot.
- Sweep and clean: Keep debris removed so that you can see when and where repairs are needed for good parking lot maintenance.
- Seal: An asphalt parking lot needs to be resealed every two to three years to preserve the resilience and inhibits weathering.
- Striped: The stripes on a parking long should be repainted every two to three years, keeping them defined visibly.
- Fill cracks and potholes: Good parking lot maintenance includes keeping cracks filled and sealed will prevent debris and water from penetrating the surface layer and causing more damage and creating potholes.
- New asphalt overlay: You can extend the life of your asphalt parking to by having the top layer stripped off and a new layer installed. This keeps your parking lot looking new longer, and value add to your property.
- Repave: When an asphalt parking lot starts crumbling, reconstruction and repaving is needed every ten years if proper and routine parking lot maintenance has been done.
How long do asphalt parking lots last?
The old saying that nothing lasts forever holds true for asphalt parking lots too. The time will come when you have to ask yourself, and a professional paving contractor, if repairing the current parking lot is sufficient. If you have kept a regular routine of parking lot maintenance, an asphalt parking lot can last up to thirty years.
Sometimes, resurfacing a parking lot is not the answer, and it is the lot’s base that makes that determination. If the base layer is damaged, then resurfacing may put a coat of lipstick on it and look better, but that lipstick is going to crack and fall off. When parking lot maintenance has been ignored and small issues fixed, it begins to fail. There may be issues with the underlying design or a construction issue or the sub-soil.
Besides proper parking lot maintenance, once a parking lot has reached the twenty year mark, it is one-fourth of its lifespan. If there is significant damage, resurfacing the entire parking lot is the best decision that will get you the most ROI.
How often should parking lots be sealed?
Typical recommendations for commercial property parking lot maintenance, sealcoating every three year is adequate for protection and aesthetics. Find a professional pavement contractor that can set up schedule parking lot maintenance in addition to your own daily routine of parking lot maintenance .
How do you maintain an asphalt parking lot?
There are many responsibilities when you own a commercial property. The four most basic assets with a commercial property are:
- The Roof
- The HVAC system
- The Elevator
- The Parking Lot
Of those four, it is the parking lot that make the first impression of the business. It may surprise many businesses owners how much business they lose because the parking lot looks like, and drives like, a battle ground. There are three categories to asphalt parking lot maintenance:
- The Must: This category concerns property and personal liabilities. Potential hazards like a broken curb, large cracks, a raised sidewalk, potholes, alligatored areas, and failing inlets.
- The Should: This category is the preventative maintenance measures that extend the lifespan of your parking lot and staying ahead of bigger problems by taking care of small issues like crack sealing and seal coating.
- The Could: Budgeting to reconstruct the parking lot area before it is needed to avoid more expensive milling and paving.
Within those three categories, parking lot maintenance is a must and should include the following:
- Seal coating
- Crack sealing
- New striping
- Proper signage
- Pothole repairs
- Inlet repair
- Remedy cause of standing water
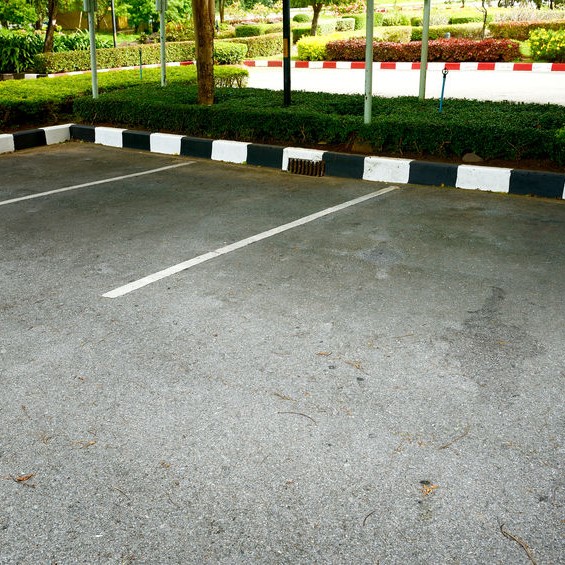
How do you maintain asphalt?
To get the most ROI, longer lifespan, and best appearance of your commercial property, daily, weekly, monthly parking lot maintenance should include a thorough cleaning. A stiff broom and powerful water hose spray will remove surface debris and dirt. Have a seal-coat every two years, no longer than every five years. Have repairs made to crack and potholes as soon as they are noticed. Last but not least, use the proper material for repairs and sealing. This is not the place to cut back and save a few dollars. Get help with your parking lot today when you call 254-716-8685!